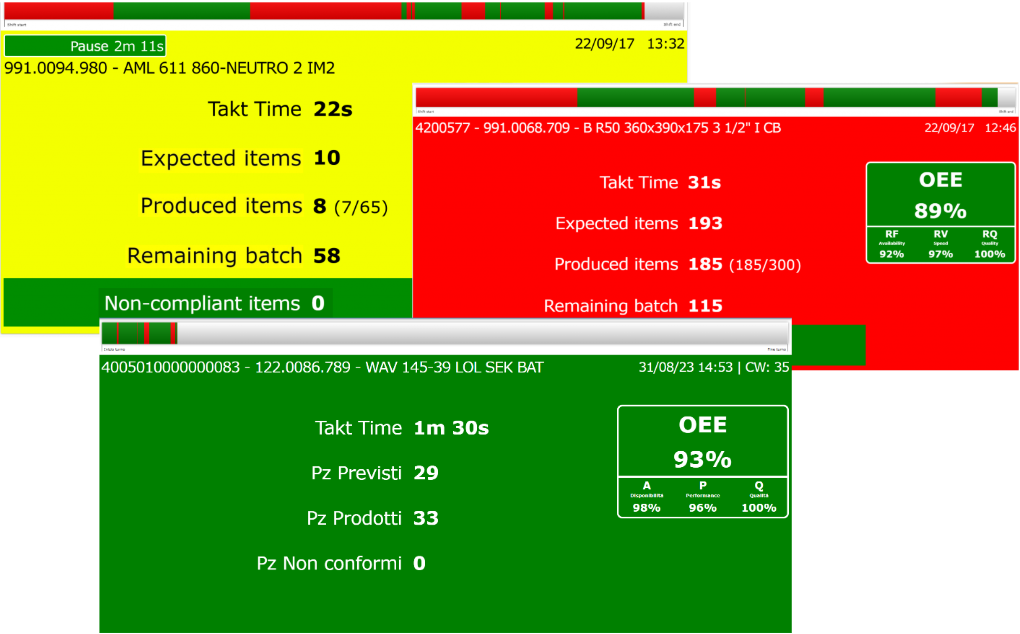
I dati di produzione
Gli Andon board mostrano i principali dati di produzione.
I colori diversi dello sfondo forniscono una immediata percezione dell'andamento della produzione, in quanto sono associati a diverse fasce percentuali dell'OEE.
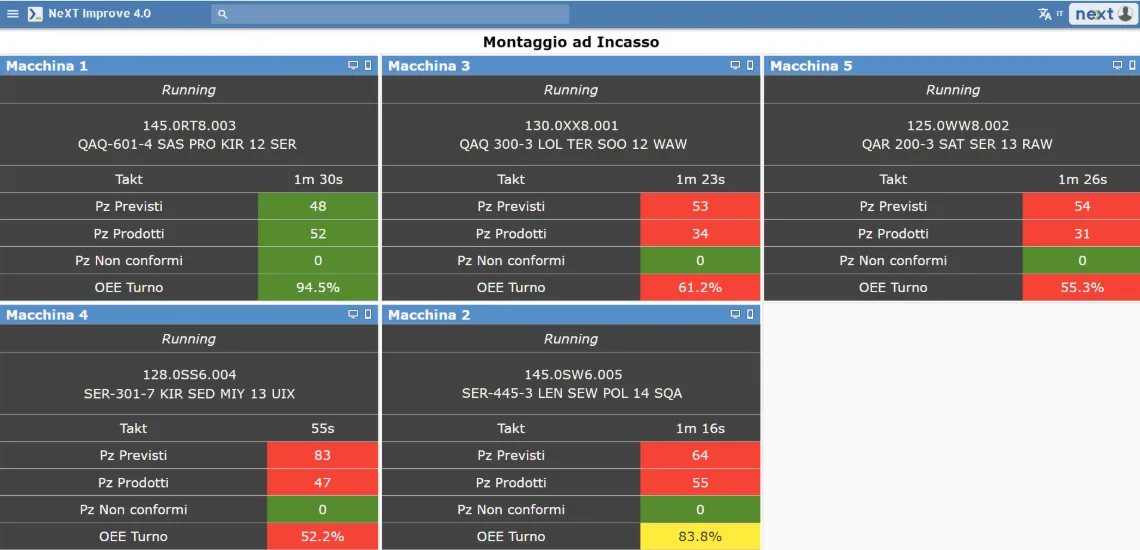
Dati aggregati
Le informazioni vengono fatte fluire in dashboard diverse, dedicate a ruoli e mansioni diverse.
Una dashboard è dedicata a mostrare i dati aggregati riguardanti tutte le linee, per avere una visione generale del reparto. È poi possibile andare nel dettaglio di ciascuna linea.