Introduzione
In questo post vogliamo spiegare cosa intendiamo quando diciamo che, attraverso i nostri prodotti software supportiamo le metodologie WCM, ovvero il World Class Manufacturing.
Andremo quindi a spiegare come e perché nasce il WCM, come funziona e quali sono gli obiettivi che si pone.
In questa maniera, sarà più chiaro comprendere anche gli obiettivi che ci poniamo noi come azienda in rapporto ai nostri clienti, cioè quali sono i risultati che ci proponiamo di far loro ottenere con i nostri software.
E soprattutto, tutti potranno apprezzare come, gli strumenti WCM, possono essere utili anche alle aziende che non fanno parte del WCM.
Buona lettura!
Come nasce il WCM
Prima di descrivere in cosa consista il World Class Manufacturing (WCM), è bene chiarire da cosa nasce e perché nasce questo nuovo modo di pensare l’attività manifatturiera.
È difficile comprendere la nascita e l’affermazione del World Class Manufacturing senza analizzare il periodo nel quale si è sviluppato.
Parliamo ovviamente di un arco di tempo recentissimo e che conosciamo molto bene, nel quale la concorrenza è sempre più “agguerrita” e i trend economici generalmente non molto positivi. Le sfide da affrontare, soprattutto per chi si occupa di attività manifatturiera, sono molteplici e complesse e passano tutte dall’aumento dell’efficienza, della qualità, dalla riduzione degli sprechi e dall’investimento nell’innovazione e nella ricerca.
Dato questo scenario, aderire al World Class Manufacturing significa ripensare totalmente il processo produttivo affinché l’ottimizzazione degli sprechi vada a realizzarsi non solo in sede di trasformazione del prodotto, ma anche in altri “momenti” della catena produttiva: anche e soprattutto in quei momenti nei quali non si crea alcun valore aggiunto per il cliente. Parliamo quindi delle movimentazioni, delle scorte, dei controlli, dei difetti, delle attese, degli errori, delle riparazioni, delle manutenzioni ecc…
Il concetto di valore quindi cambia radicalmente:
Tutte le fasi che accompagnano il prodotto, dall’inizio alla fine, devono concorrere a “creare valore”, cioè a realizzare un qualcosa per cui il cliente è disposto a pagare. Ciascuna fase.
In buona sostanza, la filosofia del WCM è cercare di creare un prodotto che possa vincere sul mercato. Come?
Alta qualità ad un prezzo competitivo.
Competitivo perché frutto di una riduzione dei costi, figlia della riduzione degli sprechi.
Il World Class Manufacturing: breve storia
Il metodo WCM è stato sviluppato negli Stati Uniti negli anni ’90. In Italia viene introdotto dal gruppo FIAT (poi FCA, oggi Stellantis) attorno al 2005 ed è considerato alla base della recente svolta positiva.
Il metodo WCM è un insieme coerente di metodologie che sono state implementate a partire dalla seconda metà del 1900.
Una metodologia che occorrerà sicuramente citare è la lean production o Toyota Production System che, attraverso i propri principi costituì una sorta di rivoluzione rispetto alla mass production di Henry Ford. Ciò che la lean production porta nel WCM è sicuramente l’orientamento al cliente, producendo solo ciò che chiede il cliente (logica pull), creando un flusso continui che permetta al prodotto di uscire dalla fabbrica il prima possibile. Il vincolo al cliente, permette di generare output solo quando il cliente richiede il prodotto, evitando quindi di creare troppo magazzino. L’altro principio lean di cui il WCM si è impadronito, è la ricerca della perfezione: il WCM, vuole migliorare le performance del processo produttivo eliminando gli sprechi e migliorando la qualità.
Ma a migliorare non deve essere solo la qualità: fanno parte del programma di miglioramento anche la sicurezza, le condizioni di lavoro delle persone, il rispetto per l’ambiente.
Un approccio WCM prevede una forte interazione con tutta l’organizzazione della fabbrica, e con tutto il personale, il quale, è importante sia motivato:
“[Il WCM]… richiede che i lavoratori si identifichino come appartenenti a una comunità e riconoscano la conoscenza come un patrimonio comune, da accrescere e gestire assieme all’impresa, un patrimonio cui tutti possano attingere e al quale tutti siano chiamati a contribuire, e l’innovazione che ne deriva come il frutto di quel comune patrimonio. [Leonello Tronti]”
Il coinvolgimento delle persone riguarda anche l’accento che la metodologia WCM pone sull’importanza della sicurezza: l’infortunio di una persona diventa un danno enorme per l’azienda.
Quindi diremo, riassumendo, che il WCM si applica a tutti gli ambiti della produzione.
Lo scopo è quello di ottimizzare i risultati facendo leva sull’idea del miglioramento continuo..
- ..dei processi;
- ..della qualità del prodotto;
- ..della riduzione dei costi di produzione;
- ..della riduzione degli sprechi;
- ..del coinvolgimento e della motivazione dei lavoratori;
- ..della sicurezza degli stessi.
Oltre alla lean production, un’altra metodologia assorbita dal WCM è il Six Sigma.
Si tratta di un termine statistico ed indica una gestione della qualità basato sul controllo dello scarto quadratico medio (indicato con la lettera greca Sigma). L’obiettivo è quello di diminuire la variabilità sui processi produttivi che può causare scarti e difetti (3,4 parti difettose per milione), cercando quindi di raggiungere un livello qualitativo il più alto possibile.
Altra metodologia importante per il WCM, sempre ereditata da Toyota, è il TPM, Total Productive Maintenance. Questo metodo mira a prevenire i guasti delle macchine piuttosto che correggerli al momento del guasto. In questa maniera diminuiscono drasticamente i fermi delle macchine e quindi di conseguenza i blocchi alla produzione.
Organizzazione del WCM
Il WCM viene raffigurato come un tempio retto da 10 pilastri tecnici (pilar).
Ciascuno di questi pilastri affronta un tema e rappresenta un ambito di intervento in area tecnica:
- Safety – Sicurezza del Posto di lavoro
- Cost Deployment – Fonti di perdita economica
- Focus Improvement – Miglioramento Focalizzato di uno specifico problema
- Autonomous Maintenance – Workplace Organization
- Professional Maintenence – Manutenzione professionale
- Quality Control – Controllo Qualitativo
- Logistic / Customer Services
- Early Equipment Management, Early Product Management – Strategia di acquisizione dei mezzi di lavoro / processi
- Enviroment – Ambiente e sfruttamento servomezzi energetici
- People Development – Sviluppo delle competenze del personale
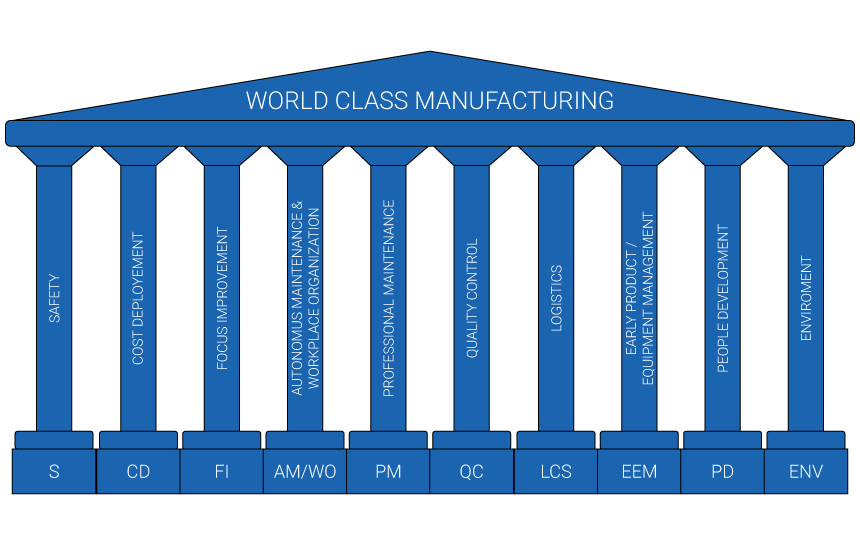
A questi pilastri tecnici seguono anche 10 pilastri manageriali. I pilastri manageriali o gestionali, costituiscono le azioni che deve svolgere il WCM leader o il direttore di stabilimento, finalizzate al favorire l’impegno e l’autoresponsabilità dei vari preposti ai singoli pilastri di attività.
- OPL One Point Lesson
- SOP Standard Operating Procedure
- SMP Standard Manutentive Procedure
- 4M MAN/METHOD/MATERIAL/MACHINE metodo di scomposizione del problema per identificare le aree sensibili
- 5W 5 WHY porsi ed iterare domande sul perché di un fenomeno
- 5W+1H WHAT/WHERE/WHEN/WHICH/WHO/HOW posizionare il fenomeno nell’ambito di questi item
- 3M valutazione oggettiva del posto di lavoro
- KAIZEN progetti specifici di miglioramento
- KPI Key Performance Indicators – Indicatori oggettivi dei risultati
- KAI Indicatori delle attività (vedi Kaizen)
Il sistema prevede una serie di valutazioni periodiche da parte di auditor certificati per verificare i risultati ottenuti dallo stabilimento. I migliori stabilimenti ricevono certificazioni che sono di quattro tipi:
- bronzo
- argento
- oro
- world class
Obiettivi del WCM
Gli obiettivi del WCM è raggiungere il valore “zero” in diversi ambiti: i difetti, le scorte, le inefficienze, i fermi, la burocrazia, l’insoddisfazione del cliente, ecc…
Ovviamente, per raggiungere lo zero, il miglioramento deve essere continuo.
Ma cos’è che guida il miglioramento continuo?
IL CLIENTE
L’azienda world-class, come già detto, è orientata al cliente. È aggressivamente concentrata sul cliente onde eliminarne l’insoddisfazione. Per questo è necessario conoscerlo e offrire un servizio eccellente.
Anche per questo il miglioramento deve essere continuo: il cliente è un’entità dinamica. Cambia continuamente, cambiano i suoi desideri, le sue domande, i suoi standard. E l’azienda world-class deve cambiare insieme al cliente e alle sue domande.
Gli insegnamenti del WCM
A corollario degli obiettivi che il WCM si pone, sta il necessario coinvolgimento del personale, a tutti i livelli: tutti devono avere ben chiari gli obiettivi.
Ed agire di conseguenza.
Quindi, possiamo evincere che, se c’è un concetto che, magari in maniera indiretta, ci insegna il WCM, è che la più grande risorsa per un’azienda non è legata alla tecnologia, ma è costituita dalle persone: il WCM arriva a coinvolgere tutto il personale a tutti i livelli, dall’operaio, al manager, al leader di pilastro.
Volendo riassumere quanto abbiamo detto, potremmo affermare che il metodo WCM, è un lavorare sulle persone.
E sulle loro potenzialità.
I nostri obiettivi
Dopo questa breve carrellata di nozioni sul WCM (ci sarebbe tanto da dire e da approfondire, ma non è questa la sede) speriamo sia più chiaro l’ottica con la quale sviluppiamo i nostri prodotti.
Fornire software a supporto di metodologie WCM, come il nostro IMPROVE 4.0, significa fornire quegli strumenti che consentono alle aziende di migliorare l’efficienza produttiva, di ricavare dati oggettivi legati alla produzione, ai fermi, alle perdite di qualità e tutto quanto possa consentire ad un manager di prendere le migliori decisioni in vista di un miglioramento continuo delle performance produttive dello stabilimento.
Collaborare con aziende-world class significa adeguare i propri prodotti alle specifiche del cliente. Significa adeguare i propri obiettivi agli obiettivi WCM del cliente.
Se vi interessano i temi che affrontiamo, iscrivetevi alla nostra Newsletter, per rimanere sempre aggiornati sui contenuti che pubblichiamo.
Ci piacerebbe conoscere il vostro parere. Seguiteci su Linkedin!
Ma se volete seguirci nella maniera più veloce e agile, seguite il nostro canale su Telegram!