Vantaggi
Contenuti del VISUAL SOP
I contenuti del Visual SOP sono organizzati in vere e proprie 'playlist', strutturate per postazione, categoria di articoli e singoli articoli. Ogni playlist segue una sequenza precisa e funzionale, in modo da presentare i contenuti in ordine logico.
I contenuti possono includere diversi formati, come PDF, immagini, video e URL. Inoltre, sono interattivi e scorrono automaticamente secondo tempi e sequenze predefiniti, con la possibilità per l'operatore di mettere in pausa il flusso di informazioni quando necessario.
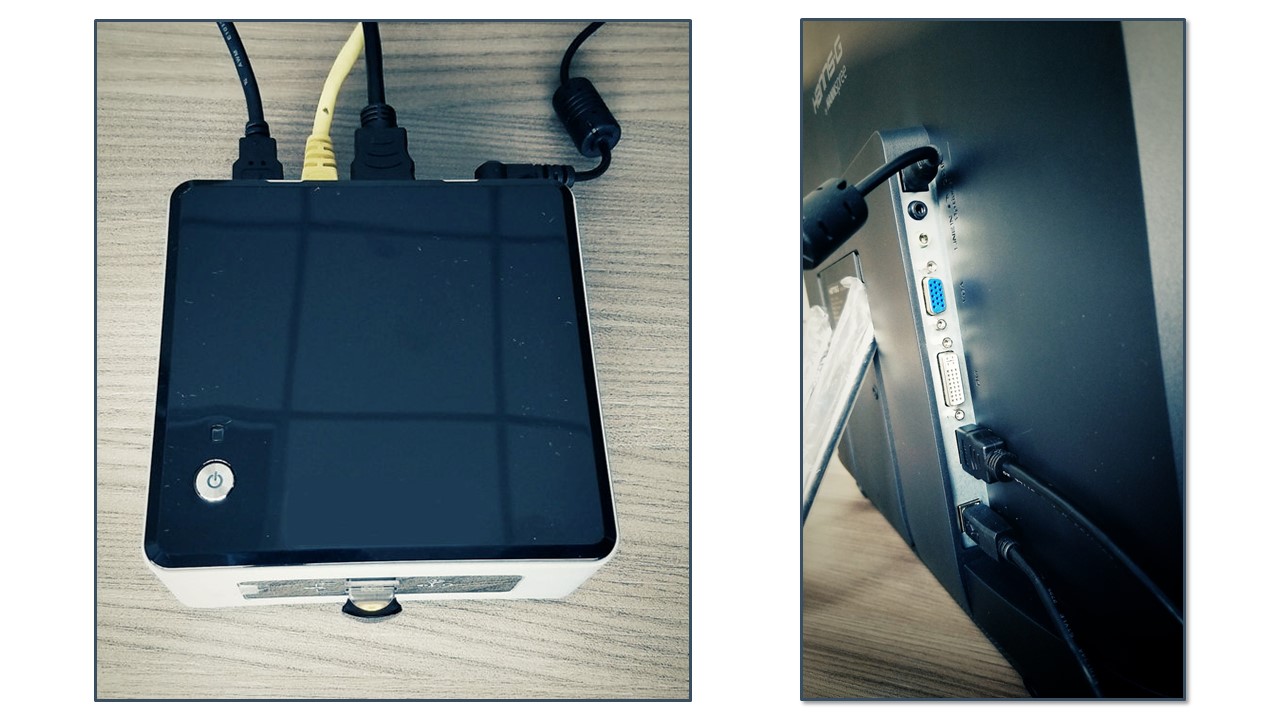
Hardware
Per implementare il Visual SOP, è necessario disporre di un monitor, un mini computer (ad esempio un NUC) e una connessione Internet.
Il monitor e il mini pc sono collegati tramite il cavo di alimentazione, un cavo HDMI per la visualizzazione delle informazioni e un cavo USB per la gestione dei dati.
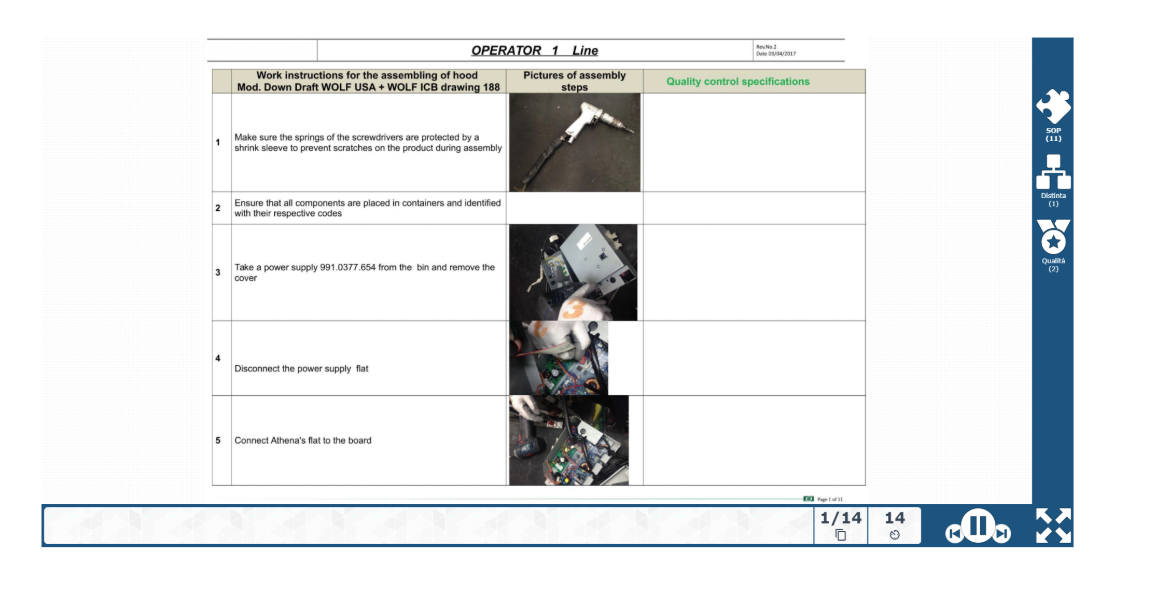
Interfaccia grafica
L'interfaccia del Visual SOP presenta un'ampia area centrale, dedicata esclusivamente alla visualizzazione dei contenuti. Sulla destra si trova un menù che permette di navigare tra le diverse categorie della playlist.
Nella parte inferiore dello schermo, invece, sono presenti il menù di navigazione per passare da un contenuto all'altro, il display del tempo rimanente per il contenuto successivo e il pulsante per ingrandire il contenuto a schermo intero.