Il Settore Automotive: L'Esperienza di Next nella Produzione Automobilistica
La nostra prima collaborazione significativa è iniziata nel 2015 con lo stabilimento Stellantis di Cento. Recentemente, abbiamo ampliato la nostra rete di partnership, collaborando con Raicam, azienda leader nella progettazione, sviluppo e produzione di freni, frizioni e attuatori per l’industria automobilistica.
Le nostre competenze e soluzioni per il settore automotive si articolano in quattro principali aree:
L’esperienza NeXT si può declinare nelle seguenti 4 macro-voci:
- Tracciabilità del prodotto
- Sequenziazione della produzione
- Gestione approvigionamento Kit componenti
- Guida all’assemblaggio dei motori
Vantaggi
Nel settore dell’Automotive, IMPROVE garantisce una migliore gestione della produzione, implementando un sistema JUST IN TIME, in particolare per i Kit di approvvigionamento o dei Kit dei componenti.
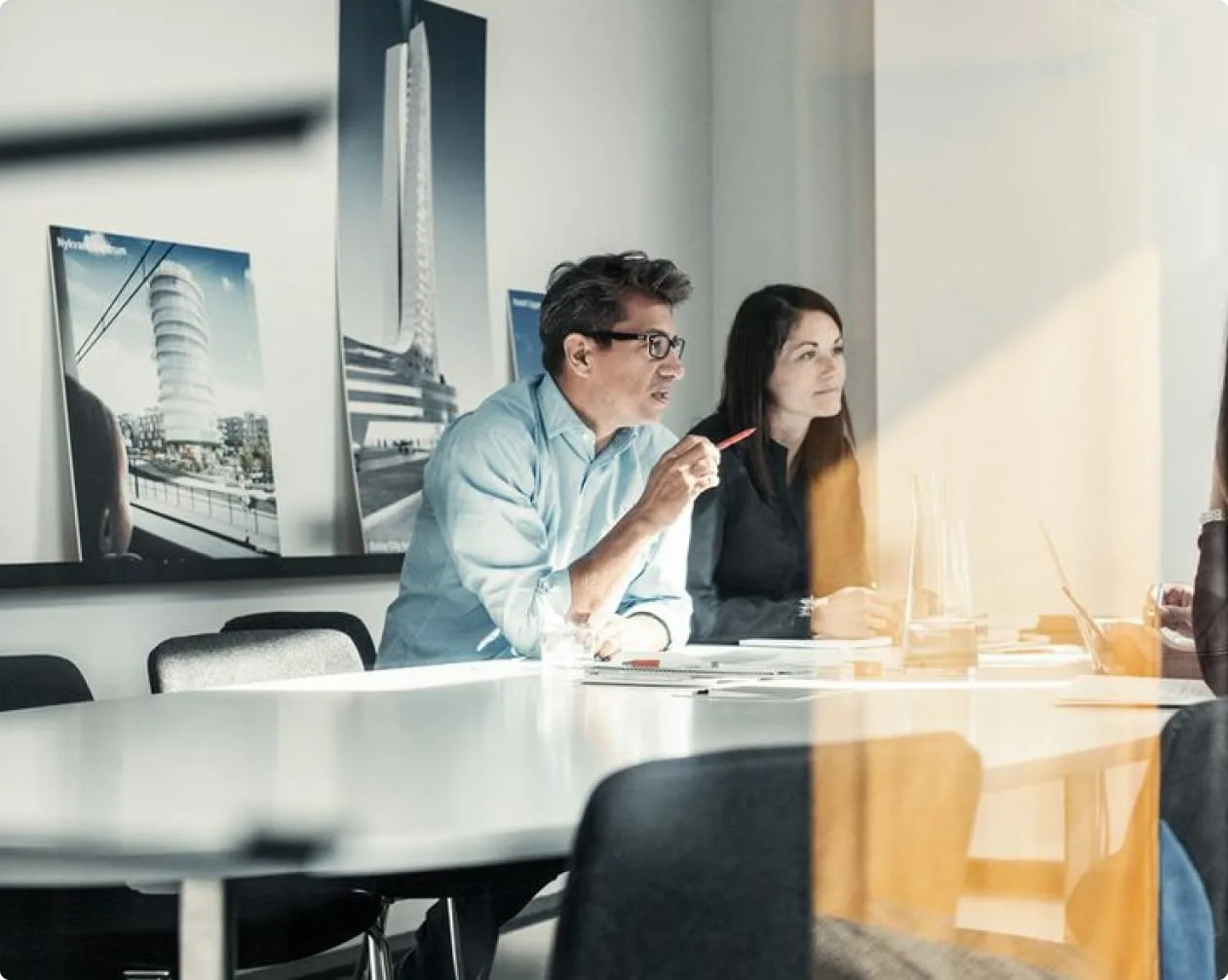
Gli obiettivi parziali
- Tracciabilità del motore e di tutti i suoi componenti
- Identificazione non conformità
- Definizione sequenza di produzione
- Sistema Just-in-time per l’approvvigionamento dei kit di componenti
- Generazione dei Kit componenti (Pick to light)
- Guida all’assemblaggio dei motori (Pick to light)
Scarica il Caso Studio
Compila il form seguente per richiedere il report completo
riguardante il caso studio del settore Automotive